There are many ways to package pharmaceutical, healthcare and cosmetic products. Each have their pros and cons. Let’s hear from Chris about the pros and cons of shrink wrapping and banding!
VIDEO TRANSCRIPT
Hello everyone! My name is Chris Anguil and welcome to the Healthcare Hot Corner, where we will be discussing topics in healthcare, pharmaceuticals and cosmetics. Today, we will be comparing Ultrasonic Banding and shrink wrap and how banding’s superior cleanliness combined with automation makes banding a more efficient and environmentally friendly choice.
Customers in pharmaceuticals and cosmetics have extremely strict standards. Hygiene, safety, efficiency, and flexibility are all essential to handling pharmaceutical products. What these industries need is an intelligent solution that covers all of these bases. Let’s take a look at an industry standard packaging process:
SHRINK WRAPPING
Packaging companies often rely on shrink wrapping technology, in which, products are bundled and shrink filmed for logistics. This process requires shrink tunnels that generate heat to shrink the film around the product. This process uses excess energy because the shrink tunnel has to be heated up, while the room itself needs to be kept cool.
When the product reaches the sales outlet, they have to be freed from the film using a knife of pair of scissors. As well as being hazardous to the person cutting through the film, there is also the risk of damaging the primary packaging while freeing the products. This again, leaves a lot of film that has to be disposed of.
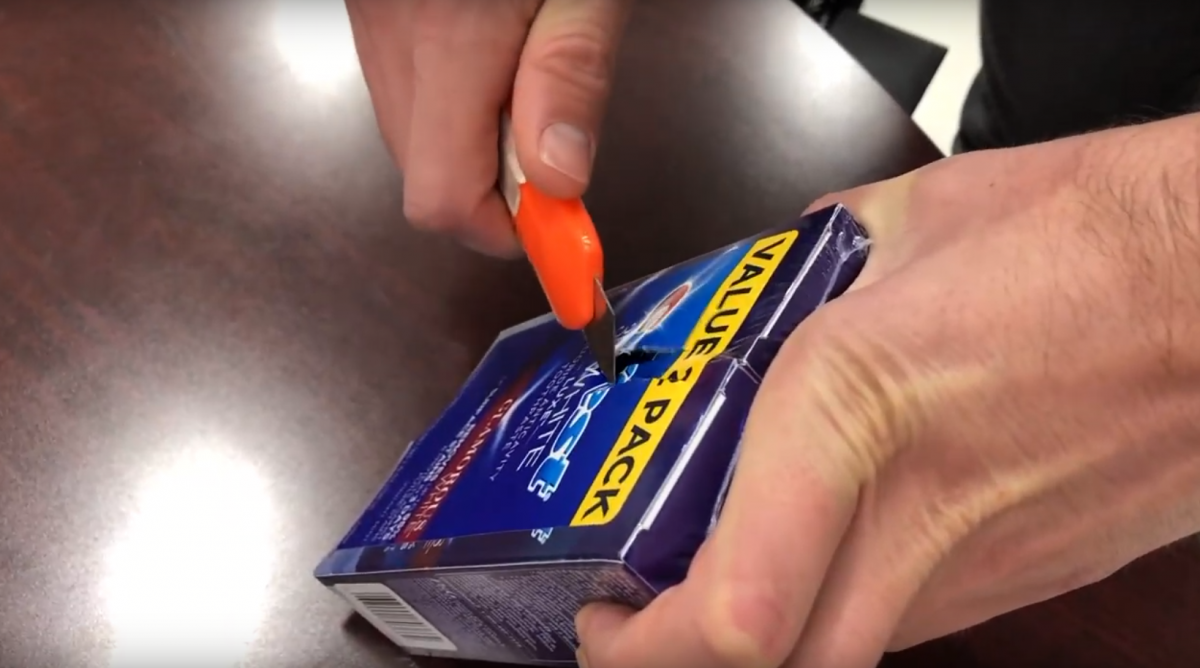
BANDING
Let us now turn to the advantages offered by the banding process. Banding is entirely automatic. The products are gently bundled with bands that are made from paper or film, as desired, and are sealed ultrasonically using our unique ATS cold-sealing technology.
As well as being safe, the process does not require heat and there is no need to use an adhesive. Banding machines can be used without the use of heat in clean rooms which cuts down on the amount of energy required and both the packaging and products benefit!
ATS banding machines can be configured for use as a stand-alone machine or as part of a packaging process where the system gets automated. In both cases, during the banding process, an integrated thermal transfer printer can print on line track and trace codes and various other pieces of information. This offers a huge amount of flexibility when preparing large or small product volumes.
Combined, these features increase efficiency and reduce the need for manual intervention which protects the packaging. The process is also safer. Overall, banding makes it much easier to handle the products at the sales outlet, as the bundles simply have to be taken out of the transport boxes.
Paper bands can be undone by hand without having to use a knife. Perforated bands can be undone by hand and bands can also be undone at the point where they were sealed. The strength of the seal is infinitely variable from slightly adherent to strong.
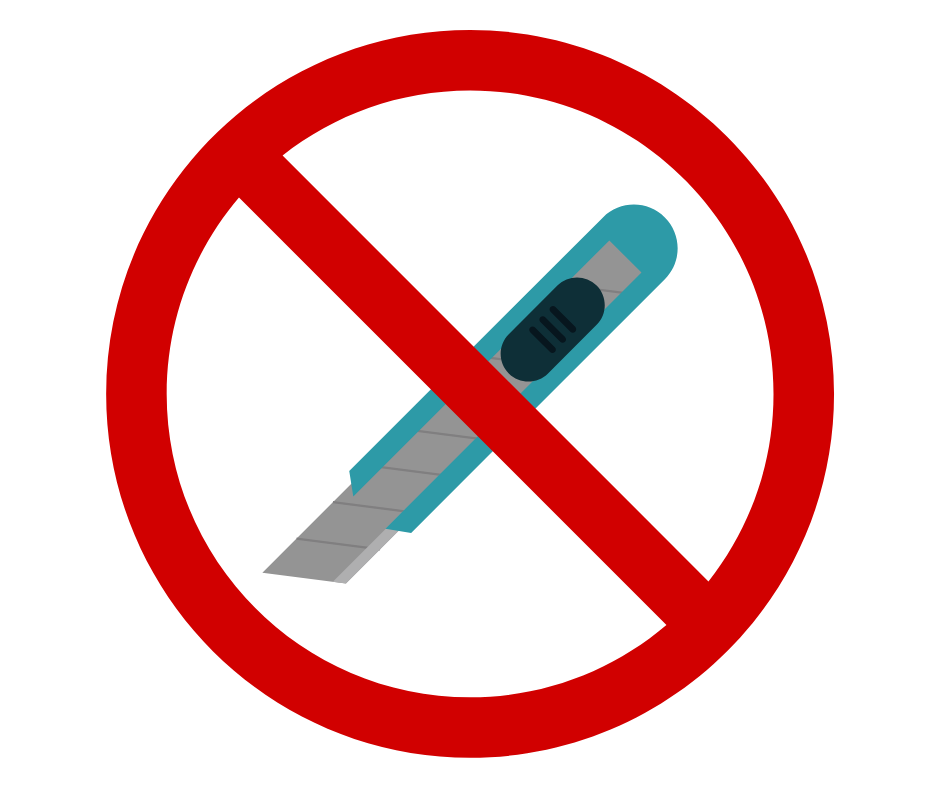
All in all, banding is cleaner and more efficient and reduces your carbon footprint!
Thanks for joining me today! Follow me on Twitter @HealthcareBands for all of the pharmaceutical packaging news you could ever want. We will see you next time!
ADDITIONAL RESOURCES
MORE INSIGHT...
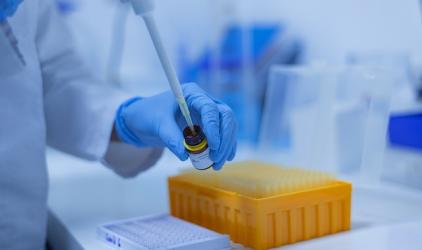
WHAT TO CONSIDER WHEN DECIDING ON PHARMACEUTICAL PACKAGING
Packaging regulations can be daunting, especially in the highly regulated world of pharmaceuticals. Ensuring that pharmaceutical products are packaged safely, securely, and in compliance with all applicable standards is not only a legal…
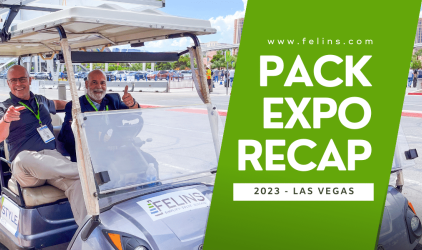
PACK Expo 2023 Recap with Felins Packaging
The Felins team is still buzzing after an incredible week connecting with industry peers and showcasing the latest packaging innovations at PACK Expo Las Vegas 2023. As the most comprehensive packaging event in the world, this year’s show did not…
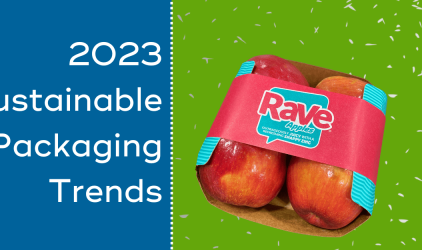
SUSTAINABLE PACKAGING TRENDS TO LOOK FOR IN 2023
INTRODUCTION Sustainable packaging is becoming increasingly important as consumers demand more environmentally-friendly products. In 2023, we can expect to see a variety of new sustainable packaging trends emerge. This blog post will explore the…