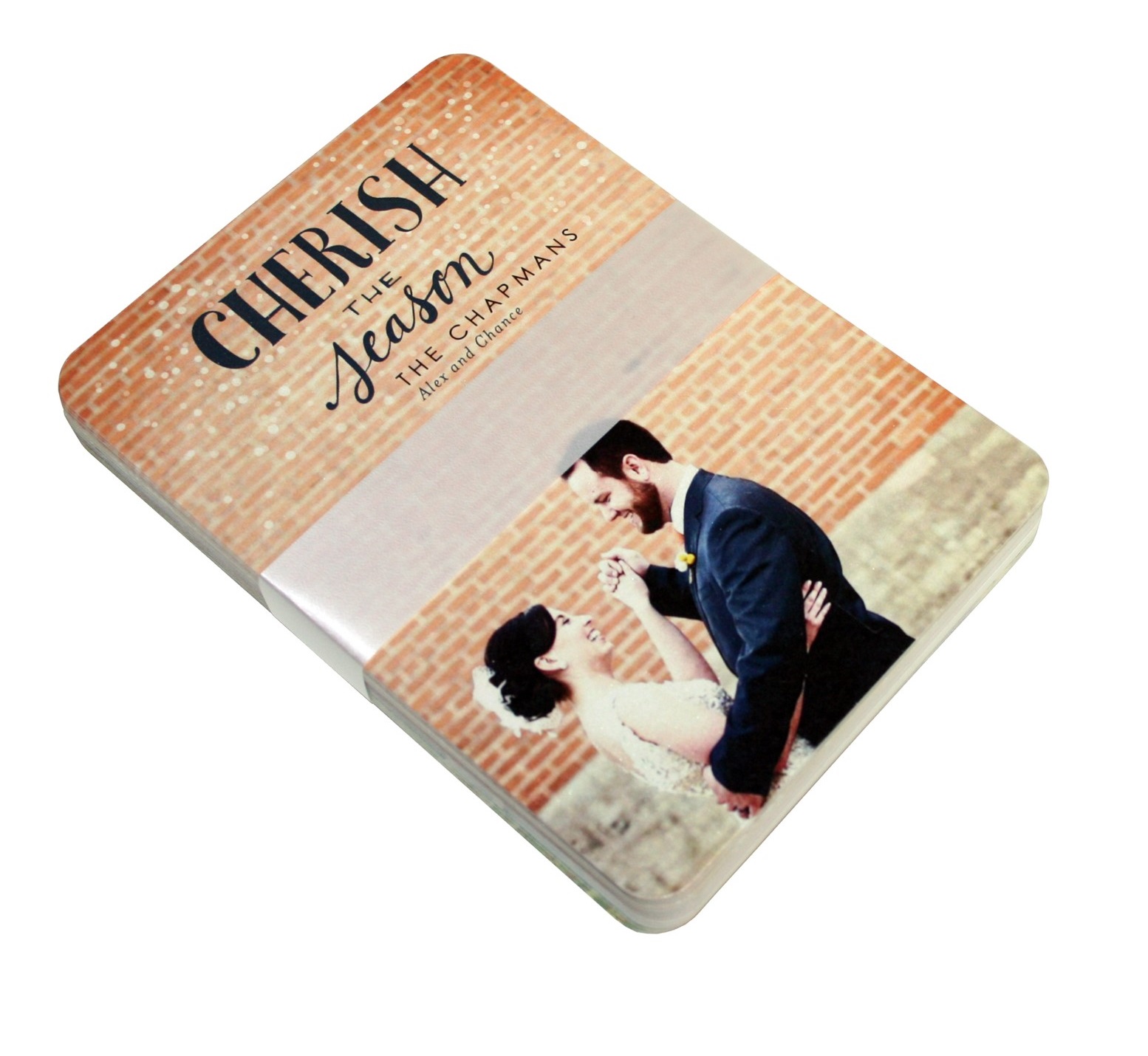
COMPANY
This company is a world-class provider of innovative label design and printing. It maintains two types of production facilities; Roll-fed and Sheet-fed. The sheet-fed facilities produce glue-applied cut-and-stack labels for many consumer products you purchase every day. This is the success story of one sheet-fed facility. (Chooses to remain anonymous.)
OFFSET-WEB PRINTER NEEDED TO IMPROVE PROCESS
The offset-web printer is a long-time user of stand alone paper banding machines and knew the efficiencies of this technology, even without automation. Because of their high volume production, their labor intensive process included sorting, hand banding, and packaging different sized cut-products. Wishing to reduce labor costs, they also wanted to deliver on end user demands for lead times and sustainability. Their goal was to gain preferred vendor status with customers by using best-in-class practices. This could be accomplished by enhancing productivity, reducing waste, and having a flexible process. The company is sensitive to their end user requests to reduce material thickness, costs, and material volumes in the end product.
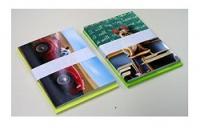
AUTOMATIC BANDING LINE SERVES TWO CUTTERS
While planning a new production flow and plant layout, the company wanted to incorporate an automatic banding machine for such items as post-cards, tickets, etc. The banding machine would service two cutting lines, so products would be of varied sizes. In order to achieve the labor savings they sought, minimal changeover was necessary.
With some design tweaks in feeding tables and accumulation areas, the CSW-DMS was successful at running the full mix of the customer’s product without time-consuming changeovers. The single machine with an extended infeed conveyor and custom-engineered product stops, allowed the machine to accept mixed stacks off two different cutters and prevented collisions from the two product streams.
The tightly banded stacks exit the bander and integrate into an auto-sortation line. The selection of a clear banding material allows product scanning for proper directing into the pack-out area without manual or human handling.
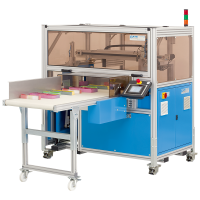
THE RIGHT SOLUTION
Felins provided an ATS® CSW-DMS corner line banding system with Shuttleworth® conveying and traffic control for the different sized bundles. The machine automatically ‘eyes’ bundle size and adjusts the band to tightly fit the bundle without damaging the product.
Results were immediate and impressive. The company improved their throughput by 60% over the hand labor process. This system had an 18-month ROI for the company. It also reduced labor needed at the banding lines.
The single banding machine with automation allowed for flexibility in the process and integration into an auto-sortation line. The company was able to reduce labor needed at pack-out.
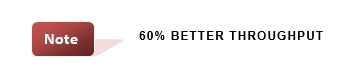
Felins® provided full operator and maintenance training on-site. In addition, a trained distributor is close to the facility and responds whenever needed.