5 WAYS TO IMPROVE PACKAGING LINE PRODUCTIVITY
Shipping and packaging speeds are faster than ever before and it can be hard to keep up. Here are 5 ways to advance your packaging line productivity.
1. IDENTIFY AND ADJUST PAIN POINTS

Safety hazards, information challenges, and ill-fitting equipment, are all common problems that slow down productivity. Take the time to identify the pain points in your packaging line. Safety hazards are costly and can hurt the reputation of the business. Information challenges slow down everything from materials going to the wrong place to machines running the wrong number of items in bundles. Machines with barcode scanners automate the information gathering and order number checking, eliminating human error. Ill-fit equipment and human error can cause machine downtime which is expensive with lost production, increased labor costs, and reputation damage due to increased delivery times and damaging customer relations.
2. BRANDING WITH BANDING
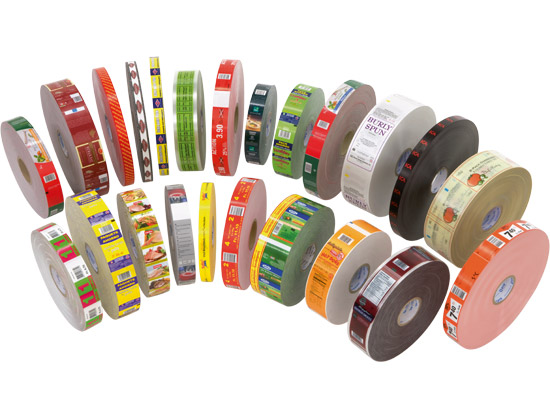
Branding with banding is when you add your logo and or product information to the material that is used to bundle your multipacks together. In addition to multipacks, these branded bands are commonly used to secure primary packaging, such as clamshells. After you have your logo on your bands you can also leave a spot for our inline printing machines to add information right before it is banded. This is helpful in the food industry for best by dates that change quickly, but is also helpful for adding batch numbers, warehouse destinations, or lot number identification. With bands up to 4” wide, options to print on the underside of the band for coupons or additional information, and support for up to 10 different colors on the band, the possibilities are endless.
3. AUTOMATION
Increasing output when there’s such a large labor shortage can be very difficult. Automation requires less employees, increases quality and reliability, and works faster than manual production lines. Automation systems can seem overwhelmingly expensive, but when you factor in reduced training costs, turnover, and injury, the ROI adds up quickly. Here’s an example of an automated counting and stacking machine for muti-packs.
4. MINIMIZE WASTE
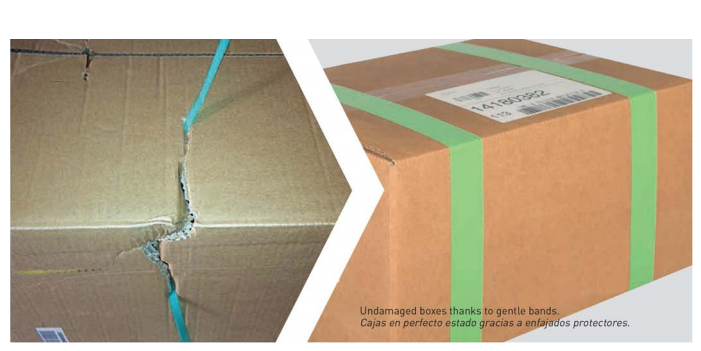
Strapping is a very strong unitizing material, but it is can be detrimental to your product. When you use strapping to secure boxes closed, rigid strapping material with inaccurate tension control often ends up ripping through boxes. This where banding comes in, with complete tension control which gives you the power to apply the precise amount of tension needed every time. Whether it’s revaluating the material you’re using or the machinery you’re using, it’s important to understand how alternatives can help you minimize waste.
5. BANDING BEFORE AUTO-BOXING
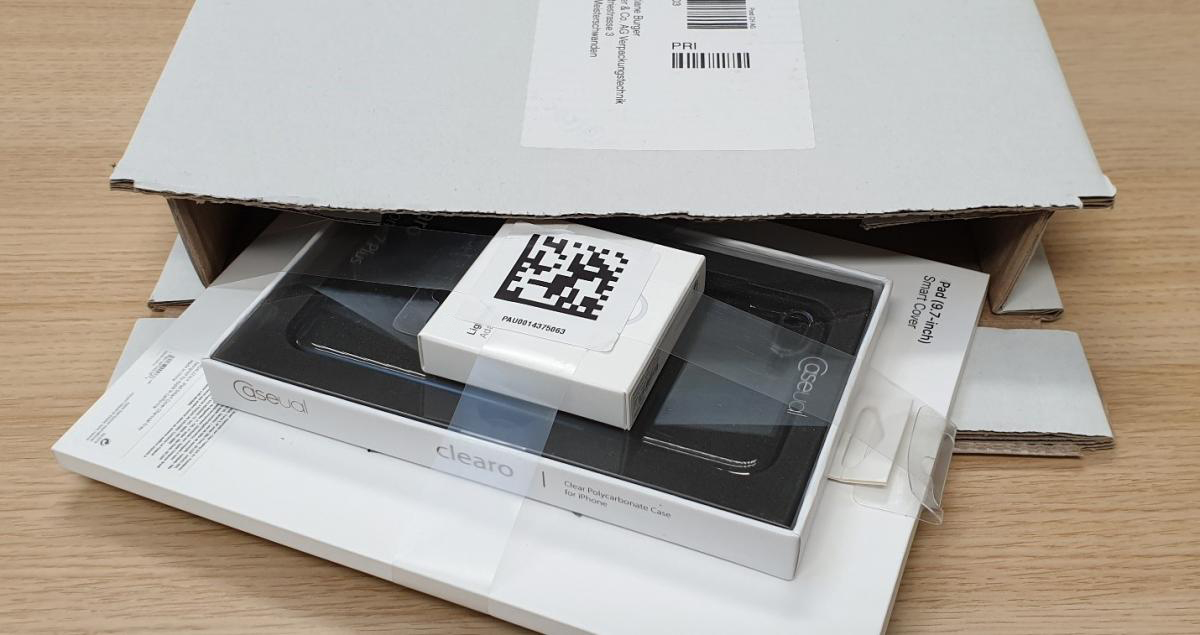
Often, e-commerce orders are more than one item. Custom size boxes are being utilized to save corrugate and void fill material. Banding before this process improves speed by being able to bundle the order with license plating, eliminating mixed up orders and jams in the conveyance system.
Interested in talking to a specialist about automation or a specific machine? Contact us here.
MORE INSIGHT...
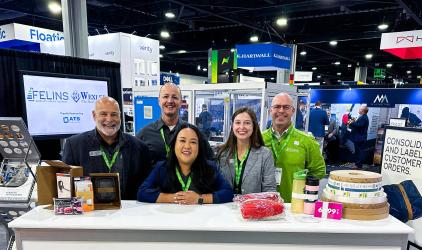
Modex 2024 Event Recap with Felins Packaging
(3 min read) The tradeshow grind never stops! Our first show of 2024 kicked off in Atlanta as our team landed in preparation for MODEX 2024, a show dedicated to the entire supply chain ecosystem with solutions in logistics, automation, robotics,…
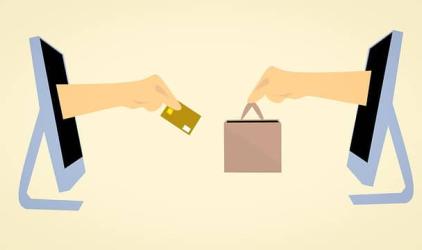
LOOK OUT FOR THESE E-COMMERCE PACKAGING TRENDS IN 2024
Discover the upcoming packaging and e-commerce trends in 2024. These changes are set to reshape the way products are packaged and delivered, focusing on sustainability, efficiency, and creative solutions. Let’s take a closer look at the…
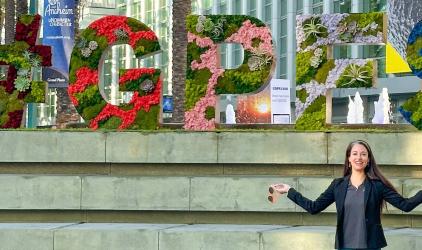
Global Produce and Floral Show 2023 – Trade Show Recap with Felins Packaging
The Felins team was thrilled to connect with fresh produce and floral packaging leaders at the vibrant Global Produce and Floral Show (GPFS) 2023 in Anaheim last week. As the premier trade show for the latest in produce and floral products as…