From multi-packs to single-serve entrees, sleeving is an excellent secondary packaging technique for branding products. Traditional chipboard and paperboard sleeves provide a sturdy option for sleeving but often require adhesives or tapes and a multi-step, labor-intensive application process.
With a banding machine, you can achieve the same (and oftentimes, better!) look as a chipboard or paperboard sleeve with much less hassle and more benefit. Let’s explain:
1. MORE TENSION.
More often than not, the adhesive or glue on a chipboard sleeve can quickly lose its strength, making the product less stable and uniform than intended for retail sale. In worst cases, adhesives can break apart and the chipboard can fall off, separating the product from nutritional information, barcodes and branding.
Our banding machines have adjustable tension so each sleeve can be as strong (or weak) as you need. And, with a strong weld, you don’t need to worry about the sleeve breaking apart or not holding the product together.
2. NO ADHESIVES, GLUES OR HEAT.
With a chipboard sleeve, you often need to use glue dots or adhesives to keep the material adhered to itself. Glue accumulates dirt, dust and debris, making your product less appealing to consumers.
Ultrasonic banding machines use an ultrasonic (aka cold) weld to adhere the banding material to itself. That means you don’t need to use ANY adhesives, tapes, glues or heat to apply the sleeves so you’ll have a cleaner, more attractive product on store shelves.
3. STUNNING GRAPHICS.
Banding material doesn’t just come in a variety of widths and thicknesses but colors as well. Combined with pre-printing options, you have nearly endless options for how your product is branded and can be confident that your graphics will be more colorful and vibrant than ever.
4. USDA & FDA APPROVED.
Our sleeve materials are USDA and FDA-approved as well as recyclable!
5. ALL-IN-ONE SOLUTION.
If you’re creating multi-packs, you’re probably counting, stacking and sleeving each pack, usually in several manually-intensive steps. With an automated banding system, your sleever can be combined with a counting and stacking unit, making the multi-packing process faster and more efficient than ever before.
You can see some of our most common food banding systems on our YouTube page.
6. SUSTAINABLE.
Today’s consumers, especially Millennials, are increasingly driven by sustainability. With buying decisions strongly affected by sustainable packaging, it’s important for manufacturers to keep consumers’ opinions in mind when developing, changing and enhancing their packaging processes.
Ultrasonic sleeving machines are a highly sustainable solution for many food processors, copackers and CPG companies. Why? Because it can combine several packaging steps into one. Because it uses less material than paperboard or chipboard sleeves. Because it requires less time and repetitive manual processes than other solutions. Need we say more?
If you’re interested in sleeving with an ultrasonic banding machine, give us a call! Our food specialists are eager to help you.
MORE INSIGHT...
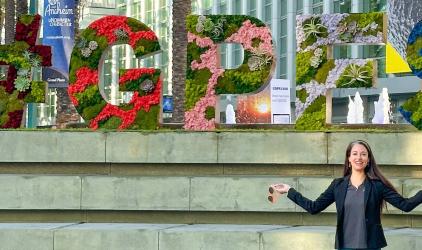
Global Produce and Floral Show 2023 – Trade Show Recap with Felins Packaging
The Felins team was thrilled to connect with fresh produce and floral packaging leaders at the vibrant Global Produce and Floral Show (GPFS) 2023 in Anaheim last week. As the premier trade show for the latest in produce and floral products as…
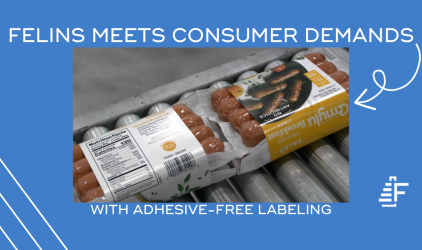
FELINS MEETS CONSUMER DEMANDS WITH ADHESIVE FREE LABELING
Richfield, WI (September 27, 2023)- In today’s retail food world, product labels do more than just provide basic information – they also create an emotional bond between consumers and brands. As such, labels play a crucial role in packaging.…
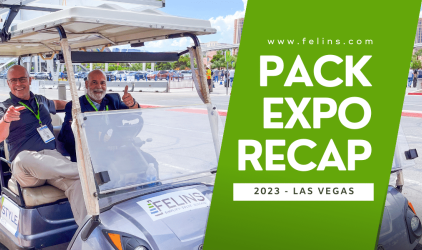
PACK Expo 2023 Recap with Felins Packaging
The Felins team is still buzzing after an incredible week connecting with industry peers and showcasing the latest packaging innovations at PACK Expo Las Vegas 2023. As the most comprehensive packaging event in the world, this year’s show did not…