Skin packs are a superior way to package protein products; however, secondary packaging is challenging with skin packs. Felins Foodie is here to help you decide what secondary packaging is ideal for all of your skin packaging needs!
VIDEO TRANSCRIPT
Welcome! This is Food for Thought with Felins Foodie.
There are many ways to package various protein products such as chicken, beef, pork, salmon, veggie burgers and more! As a consumer, when I grocery shop, I know I want to actually see the protein product before I buy it.
A rather popular form of showcasing meat products at the retail level is through a packaging form known as skin packs. Like every form of food packaging, there are direct benefits that drive the choices made by food manufacturers. One of the advantages of a skin pack, or skin packaging, is that the product remains securely fixated in the tray and doesn’t move, resulting in an excellent appearance.
Also referred to by some as vacuum skin packaging (VSP), it has been known to reduce food waste and enhance shelf life. This is because VSP eliminates oxygen used in the packaging. PLUS, the product maintains more of its moisture! In many cases we end up less materials with skin packaging due to the elimination of headspace!
Okay, so this sounds like a great form of primary packaging, but what about secondary packaging, labeling or even case packing!? This unique and premium form of packaging makes the labeling process tricky.
A typical top-seal tray can be preprinted with the labeling details such as the nutrition facts panel, cooking instructions, and more! But with the skin-tight nature of the VSP, we’re faced with a unique challenge.
Some common ways to label this form of packaging are with a sticky, manually applied label, a c-warp or full coverage label, a paperboard sleeve, or wait, get this, a band! All of these forms have their pros and cons, not just from the aspect of the marketing department, but also for the downstream team at the end of our packaging line.
Consider a sticky label: when placed on a skin pack, it wants to fall onto the highest part of the product in the skin pack tray, which has potential to deform the label. Plus, depending on the form of case packing, when trying to automate, the sticky label may not be strong enough to stick to the tray when being picked and placed into a tray, causing potential obstacles for robotics.
A sleeve, also great in appearance, being more rigid than a sticky label, may or may not adhere to the skin pack tray, meaning that this could ALSO pose a challenge for those case packers, manual or automated.
An ultrasonic sealed band is uniquely applied without adhesives but rather with tension and an ultrasonic weld providing a snug and clean looking label on the VSP, while also being secure to the tray.
If you aren’t using robotics or automated case packing right now, the industry may require it in the future and the tensile strength of banding material, married with the strength of the ultrasonic weld gives robotics a chance to pick up the skin packed trays by the band and stack them on top of each other in a uniform and consistent fashion.
Take your sleeving and labeling to the next level, with this premium label band that your end of line automation and consumers will love.
Follow me, Felins Foodie, to learn more about ways you can reduce labor and packaging waste AND improve your overall bottom line with adhesive-free labeling, sleeving, and unitizing solutions. Subscribe below!
ADDITIONAL RESOURCES
MORE INSIGHT...
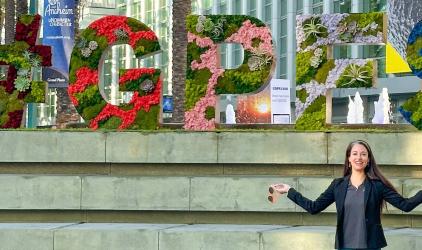
Global Produce and Floral Show 2023 – Trade Show Recap with Felins Packaging
The Felins team was thrilled to connect with fresh produce and floral packaging leaders at the vibrant Global Produce and Floral Show (GPFS) 2023 in Anaheim last week. As the premier trade show for the latest in produce and floral products as…
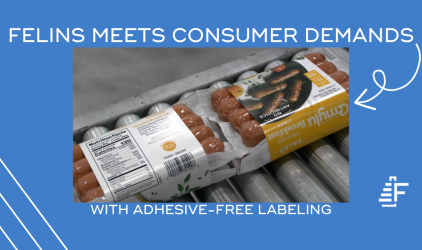
FELINS MEETS CONSUMER DEMANDS WITH ADHESIVE FREE LABELING
Richfield, WI (September 27, 2023)- In today’s retail food world, product labels do more than just provide basic information – they also create an emotional bond between consumers and brands. As such, labels play a crucial role in packaging.…
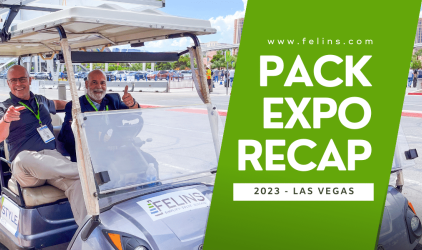
PACK Expo 2023 Recap with Felins Packaging
The Felins team is still buzzing after an incredible week connecting with industry peers and showcasing the latest packaging innovations at PACK Expo Las Vegas 2023. As the most comprehensive packaging event in the world, this year’s show did not…